News & Events
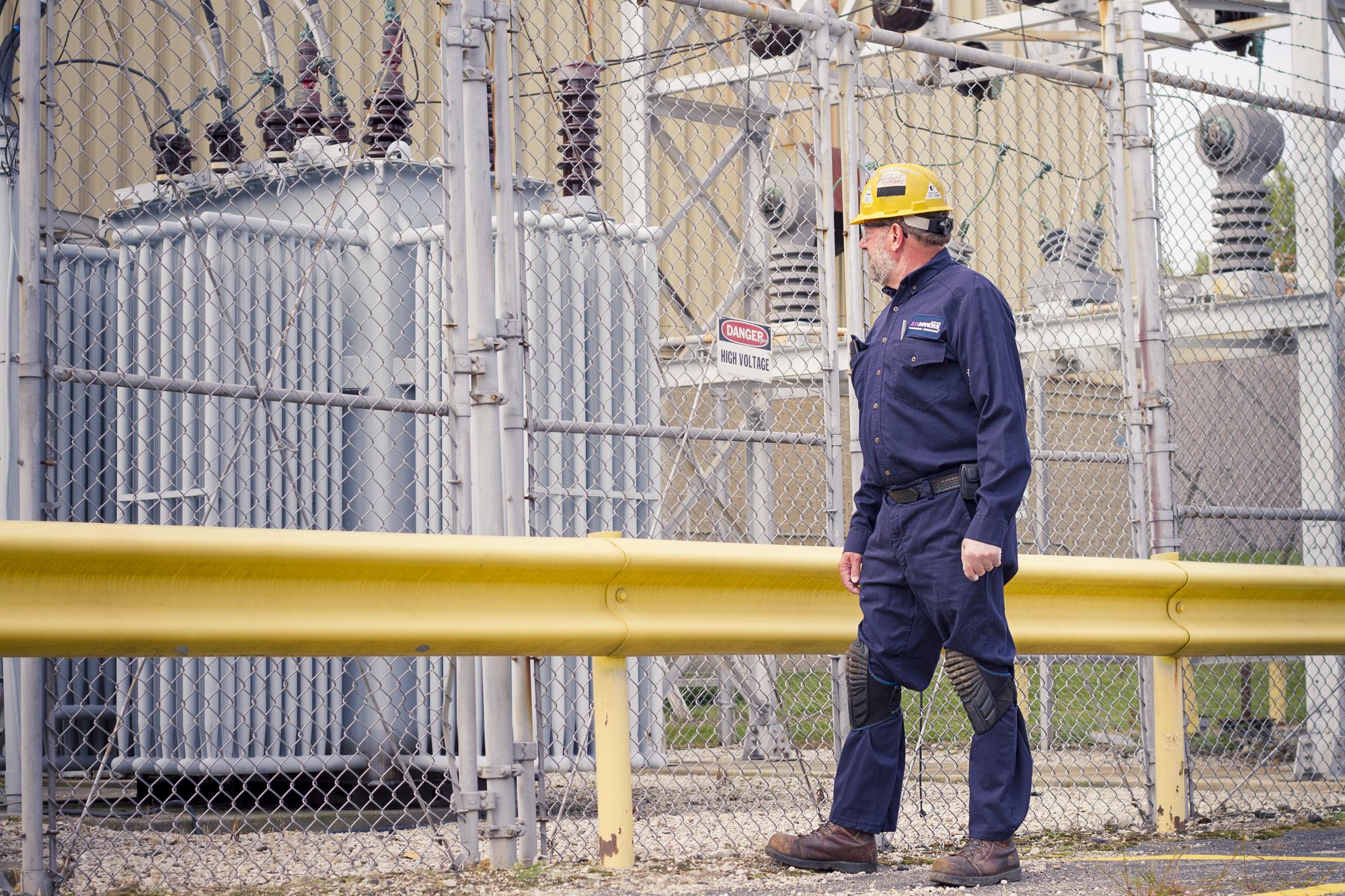
Unlock Insight into Transformer Reliability by Detecting Partial Discharges
The goal of transformer reliability is to cost effectively reduce the risk of failure. A holistically planned maintenance program does just that, using a wide variety of diagnostic methods. Conventional PMs may highlight partial discharge in certain components but may miss others which can eventually cause permanent damage.
What is Partial Discharge?
Partial discharge (PD) is a localized dielectric breakdown within a solid, liquid, or gas insulator. A full discharge is electricity traveling from phase to ground or from phase to phase, while a partial discharge is an electrical discharge that does not fully bridge the gap between two conductors. PD, if left unchecked, gets progressively worse and will eventually result in the failure of the conductor or the insulation. It should be noted that PD is not detectable using human senses at its beginning stages and is not necessarily a reliability issue.
How and where does it occur?
PD occurs naturally on medium and high-voltage power equipment due to current flowing through conductors at high voltages and often exists along the boundaries of insulating materials. PD can be found on tap changers, bushings, cables, and components inside the main tank within the transformer liquid, gas bubbles, and solid insulation.
Within these components, defects can exist for a variety of reasons, some due to manufacturing errors, over-heating, or overloading. These defects could be voids or gaps in solid insulation and conductor connections or bubbles in liquid insulation. Over time these defects can worsen due to electrical, mechanical, or thermal stresses. When defects are present, and the component cannot withstand these stresses, a dielectric breakdown occurs, resulting in a partial discharge.
Why is understanding partial discharge important?
If ignored, PD will continue to occur. As it does, the insulation will continue to deteriorate. As the PD worsens, our natural human senses (hearing, seeing, and smelling) could detect it as it becomes more prominent. As the insulation degrades, the partial discharges get larger, ultimately leading to a full breakdown and potentially catastrophic failure. To summarize, PD results from an electrical breakdown that—over time—degrades an asset’s insulation, leading to failure.
5 Methods to Detect Partial Discharges
PD can be detected due to its by-products or symptoms it leaves “behind.” Evidence of PD can be observed through changes in sound, heat, light, chemical reactions, and electrical signals. Just as dissolved gas analysis gives us the presence and concentration of dissolved gases in the oil showing fault conditions, detecting these PD by-products indicates the severity of the partial discharges.
(1) Acoustical Measurement
Partial discharges can emit sound waves that can be audible and inaudible. Using a detection device, like a directional ultrasonic microphone, one can capture sonic or ultrasonic waveforms that can help pinpoint the location and severity of the PD.
(2) Thermal Measurement
Infrared thermography helps detect PD where there is a direct line of sight to the electrical component in question. PD evidence may be observed using a traditional infrared imager by detecting thermal patterns.
(3) Optical Sensors
Optical sensors can be placed near the component to detect potential PD and diagnose defects with greater accuracy.
(4) Chemical Testing
Testing transformer oil can indicate the presence of partial discharges in the main tank. Typically, PD can be detected by taking an oil sample and performing dissolved gas analysis (ASTM D3612).
(5) Electrical Sensors
Partial discharges can induce voltage or current spikes. PD can be detected by using inspection equipment to measure the severity of these spikes or pulses, leading to a more accurate diagnosis.
What can someone do about partial discharge?
Although not all partial discharges materially degrade the insulation or component and lead to failure, they can be an early warning sign for potentially harmful PD activity. Because of this, once discovered, measures should be taken to more closely monitor the PD to determine the severity.
Once the severity is determined to affect reliability, action can be taken to repair the equipment, returning it to normal operating condition and continuing to conduct regular maintenance intervals.
How can SDMyers help?
Transformers fail, sometimes unexpectantly, and determining which transformers pose a risk for failure is difficult without consistent, reliable data covering multiple failure modes. Unfortunately, there is a limited number of detection methods (e.g., oil sampling, visual inspections, IR inspections, etc.) and a finite amount of data that can be gathered while the transformer is energized at a reasonable cost.
Because of this, it is critically important to understand the effects of partial discharge and how to detect when there might be an issue. Luckily, PD detection methods can be performed on a regular preventative maintenance schedule while the equipment remains energized as part of an overall condition-based monitoring program.
PD inspections allow transformer owners to receive the maximum data, information, and knowledge to confirm existing failure modes and identify others not easily diagnosed. SDMyers helps organizations construct a holistic PM program and consider if PD inspections make sense for their operation and maintenance philosophies. The beauty of PD detection is that it can identify a problem very early, allowing the asset owner to be more accurately informed on the condition of their asset.
June 07, 2022