News & Events
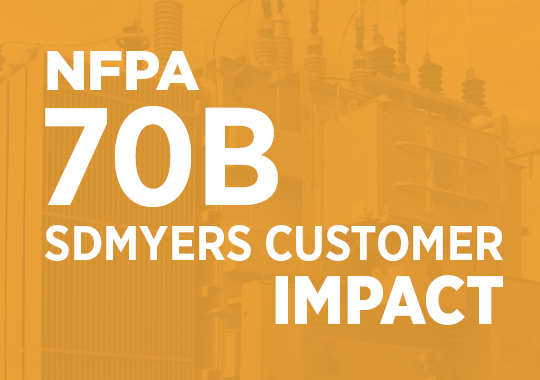
Infrared Thermography Becomes Standard for Electrical Maintenance
How Changes to NFPA 70B Impact You
The NFPA 70B Recommended Practice for Electrical Equipment Maintenance has generally been just that—a recommendation. Since its inception in 1975, it has always been categorized as a recommended practice. However, as of January 2023, it has become a recognized standard as the NFPA 70B Standard for Electrical Equipment Maintenance. The transition means the NFPA recommendations on what should be done are now standards for electrical equipment maintenance—setting the stage for OSHA to enforce what must be done.
Who is the NFPA?
The NFPA is a global authority on fire, electrical, and building safety. They produce codes and standards addressing various aspects of electrical safety and reliability, including work practices, equipment maintenance, compliance with electrical regulations, and educational materials.
What is the NFPA 70B Standard?
The NFPA 70B standard is part of the National Electrical Code (NEC) family of documents and is vital in ensuring electrical safety and maintenance standards. NFPA 70B details preventive maintenance for electrical, electronic, and communication systems and equipment to prevent equipment failures and worker injuries.
NFPA 70B Quick Facts
- Consensus standard, effective January 16, 2023
- Used in conjunction with NFPA 70 – National Electrical Code® and NFPA 70E – Standard for Electrical Safety in the Workplace®
- Not intended to supersede or duplicate manufacturers’ recommendations
- Can become the basis for many enforceable OSHA practices
- Can often be required by insurance companies as a condition for coverage
What is New in NFPA 70B Related to Infrared Thermography?
A few of the updates in the 2023 release of NFPA 70B as a standard have to do with transformer maintenance intervals and annual liquid sampling and testing. Previously, the intervals for transformer maintenance were only recommendations. As part of the change, they are now requirements that must be met.
One of the most notable updates is that infrared thermography is now an annual requirement for all electrical equipment.
“One of the most notable updates is that infrared thermography is now an annual requirement for all electrical equipment.”
Infrared thermography is a diagnostic, non-intrusive, preventative maintenance inspection technique to detect patterns and differences in thermal radiation. It is a valuable tool for detecting potential issues in electrical equipment before they become critical. The thermal images can be used to identify potential points of failure. Common points of failure can be detected by seeing patterns or differences in thermal radiation. These failure modes differ depending on the equipment type, but some include imbalanced loads, overloaded circuits, loose connections, corrosion, or defective components.
By detecting failure modes through infrared scanning and repairing them, the likelihood of a breakdown because of those failure modes can be reduced. In addition to the benefits of IR inspections, having an IR window installed on the unit ensures the safety of personnel and significantly reduces the cost of performing recurring inspections on electrical assets. This is because IR inspections through IR windows require little-to-no PM-related downtime and allow lower levels of PPE to be worn during inspections (compared to energized open panel inspections). IR windows offer a safer alternative with less time, less PPE, and less risk.
By requiring annual IR scanning for all electrical equipment, the NFPA aims to improve safety and reliability, minimizing the risk of equipment failures, fires, or other hazards associated with poorly maintained electrical systems.
Keeping You Compliant with Infrared Thermography
For the last several years, SDMyers has recommended annual IR scanning as part of regular best practices for transformer maintenance. We believe IR scanning is a safe, efficient, and cost-effective way to ensure maximum reliability and safety for your electrical assets. The NFPA 70B standardization of infrared thermography may be new to some, but it is not to us. Our field service experts and mobile diagnostic technicians are fully equipped and trained to perform IR scanning, install IR windows, and diagnose potential issues.
While transformer liquid testing is robust, it is not exhaustive. IR scanning is a proven complement that can be performed on energized equipment at the same time as liquid sampling with minimal disruption and can provide a more accurate understanding of potential failure modes.
IR Scanning + Annual Liquid Sampling = Maximum Reliability
Combining infrared thermography with annual liquid sampling and DGA testing greatly improves the accuracy of diagnosing potential issues as early as possible. Any temperature anomalies detected by the thermography can be cross-referenced with the results of the liquid analysis to provide a more complete assessment of the transformer's health. This can help to identify potential problems early and allow for timely maintenance, reduce the risk of unplanned downtime, and maximize the transformer's lifespan.
SDMyers mobile diagnostic technicians are trained and equipped to perform IR scanning—why not take advantage when they are already at your facility? Contact your Diagnostic Analytical Coordinator or fill out our contact form to get started today.
Additional Resources: Three Infrared Thermography Case Studies
BUSHING HOT SPOTS - Find out how IR scanning helped an industrial customer in New York identify a potentially unsafe, costly bushing hot spot and plan a scheduled replacement. View Case Study
MAIN TANK DEFICIENCY - IR scanning aided the Dissolved Gas Analysis for a Pennsylvania-based company, identifying a potential transformer deficiency and supporting strategic reliability planning. View Case Study
COOLING SYSTEM FAILURE MODE - See how IR scanning helped a Michigan-based customer detect low liquid levels and a faulty gauge to avoid overheating and potential transformer failure. View Case Study
May 01, 2023